APID Mk III is one of the world's first autonomous aerial vehicles for commercial use, with fully automatic vertical starting and landing capabilities. Contrary to what is common in the UAV world, it's developed for civil applications with military capability spin-offs. The result is, that the cost of an APID Mk III is a fraction of the costs of other UAV systems.
APID Mk III is a system concept for autonomus positioning and transportation in the air. The system consists of a minihelicopter, HCP 301 which is stabilized and navigated by a Flight Control System, FCS 202. The carrier is, through the Flight Control System, in radiocontact with the Ground Control Station, GCS 202 .
The system is very mobile and easy to operate. The Gound Station is housed in a covered trailer for a private car, which also carries the complete system during transfers
The system can be operated in 4 modes:
Autonomus control: The vehicle performs fully autonomusly a preloaded mission. Contact with the Ground Station is not neccesary.
Semiautonomus control: The operator is able to revise and finetune preloaded waypoints from the Ground Station by a joystick or a keyboard.
Manual control: The FCS stabilizes the attitude of the carrier but vector speed is controlled by a operator from the Ground Station by a joystick or a keyboard.
Remote Cotrol: A trained pilot on the ground RC-operates the carrier directly on its controlling surfaces without stabilization from the FCS. This mode is used as Fail safe in autonomus modes by bypassing the FCS.
The APID Mk III is first of all developed for missions with high demands on positioning accuracy and endurance in hovering positions. The system can be modified with different security solutions to suite also for missions wich demands fast removals and long action range.
Extra options for HCP are for example:
Pilotcamera controlled from the ground station.
Controlable, stabilizised platform for different payloads (a tailormade construction integrated in the system and stabilized by the FCS).
Wheeled trailer for easy movement on the ground by one person.
Service:
Before every flight: 10 minutes overhaul by the operator according to checklist 1.
Every 25:th flighthour: 60 minutes overhaul by the mechanical engineer according to checklist 2.
Every 100:th flighthour: Servicekit 1; spark plug, airfilter, fuelfilter, gearboxoil, mainrotorbearing, rotorbladebearings, cogbelt and links. 4h overhaul by the mechanical engineer according to checklist 3.
Every 500:th flighthour: Servicekit 2; exchange engine, exchange actuators (5 pcs), mainrotorblades, tailrotorblades, Strengthstressed fasten elements and vibration elements to the engine, gearbox, mainrotorhead driveshaftcouplings and to the FCS. 16h overhaul by the mechanical engineer according to checklist 4.
Data och performance:
Computer: PC-104 based Ampro-586
Max IO-kanaler: 32 analog, 32 digital, 6 serial and 10 timers
Realtimesystem: RTKernel 4.5
Softwaretool: Systembuild
Codegenerator: AutoCode/C
Sensors: 1 inertial navigation package (3 gyros, 3 accelerometers) , 1 2-axis inklinometer, 1 Compass, 1 GPS-reciever, 1 Microwavealtituderadar, 1 Infraredaltitudemeter, 1 Barometer, 2 Revolution counters, 1 Fuelmeter
Extra options for GCS 202 are for example:
Reciever for DGPS correction factors if regional DGPS system exits. (like the Swedish EPOS-system which is broadcasted by the FM-net)
Local DGPS-station (if regional DGPS-system not exists)
Equipment for communication with air traffic control
Lap top for GIS-presentation and och mission programming
Data and performance: Computer: Intel-486 industry computer
Datalink: 9600 baud radiomodem (439MHz)
APID Mk III is a system concept for autonomus positioning and transportation in the air. The system consists of a minihelicopter, HCP 301 which is stabilized and navigated by a Flight Control System, FCS 202. The carrier is, through the Flight Control System, in radiocontact with the Ground Control Station, GCS 202 .
The system is very mobile and easy to operate. The Gound Station is housed in a covered trailer for a private car, which also carries the complete system during transfers
The system can be operated in 4 modes:




The APID Mk III is first of all developed for missions with high demands on positioning accuracy and endurance in hovering positions. The system can be modified with different security solutions to suite also for missions wich demands fast removals and long action range.
Carrier HCP 301 :
HCP 301 has been developed for a payload of 20kg. The carrier is very easy to handle, operate and serve. The rotorsystem is of Bell/Hiller-type with mainrotor, stabilisator and tailrotor. Regulation of the vehicle is carried out by 5 actuators; 3 on the mainrotor, 1 on the engine and 1 on the tailrotor.
The body is a weigth optimized construction of carbonfiber composite. The rotors are driven by a 1-cylinder, 2-stroke petrolengine through a driveshaft, a cogbelt and a gearbox. The engine,the transmission and the rotorsystem is vibration isolated from each other and from the body with gives a minimum of disturbance to sensors, electronics and payloads. The construction also permits an extra vibration isolated suspension of the FCS in the inertial center of the carrier and suspension of different payloads on the downside of the carrier.
The landing gear is elastic in order to reduce ground resonance and shocks when starting and landing. The legs are equipped with surfaceexpanding discs for start and landing on soft and hard surfaces.
HCP 301 has been developed for a payload of 20kg. The carrier is very easy to handle, operate and serve. The rotorsystem is of Bell/Hiller-type with mainrotor, stabilisator and tailrotor. Regulation of the vehicle is carried out by 5 actuators; 3 on the mainrotor, 1 on the engine and 1 on the tailrotor.
The body is a weigth optimized construction of carbonfiber composite. The rotors are driven by a 1-cylinder, 2-stroke petrolengine through a driveshaft, a cogbelt and a gearbox. The engine,the transmission and the rotorsystem is vibration isolated from each other and from the body with gives a minimum of disturbance to sensors, electronics and payloads. The construction also permits an extra vibration isolated suspension of the FCS in the inertial center of the carrier and suspension of different payloads on the downside of the carrier.
The landing gear is elastic in order to reduce ground resonance and shocks when starting and landing. The legs are equipped with surfaceexpanding discs for start and landing on soft and hard surfaces.
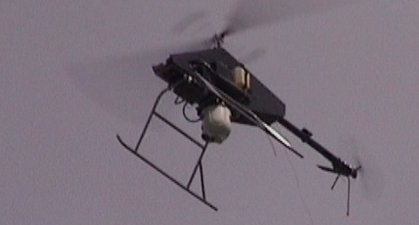
Extra options for HCP are for example:



Length: 2,9m
Body: Carbonfiber composite, Weigth 5kg
Mainrotor: Twobladed glasfiberrotor (diameter 2.9m) with Hiller stabilisator. 900rpm
Dryweight: 35kg
Maxweight: 55kg
Engine: 1cylindric, 2-stroke, 125cc, 9500rpm
Enginepower: 14Hp
Fuel: Petrol 95 octane leadfree, 2% 2-strokeoil
Speed: 0-100km/h
Range: 100km (with 8l petrol and maximum 12kg payload)
Start: Electrical
Power supply: Generator 300W
Mainvoltage: 24V (18-36V)
Backup: Battery 60Wh
Body: Carbonfiber composite, Weigth 5kg
Mainrotor: Twobladed glasfiberrotor (diameter 2.9m) with Hiller stabilisator. 900rpm
Dryweight: 35kg
Maxweight: 55kg
Engine: 1cylindric, 2-stroke, 125cc, 9500rpm
Enginepower: 14Hp
Fuel: Petrol 95 octane leadfree, 2% 2-strokeoil
Speed: 0-100km/h
Range: 100km (with 8l petrol and maximum 12kg payload)
Start: Electrical
Power supply: Generator 300W
Mainvoltage: 24V (18-36V)
Backup: Battery 60Wh
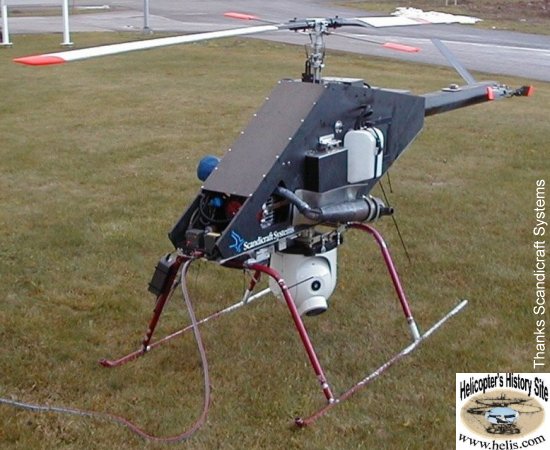
Service:




Flight Control System FCS 202
FCS 202 consists of a computer, a number of sensor and a power supply unit. The mainpart of the FCS 202 is packaged in a central unit which is to be placed vibration isolated in the inertial center of the carrier. The central unit is complemented by a number of decentralized sensors mainly located to the tailbar.
The software of the FCS 202 is developed for fully autonomus flight control with indata from optional sensors. The extremely open arcitecture make the system very open to adding functionalities, for example active vision and higher levels of intelligence.
By qualified filtering and well balanced regulators the FCS is able to control the carrier with extremely high precision also by using relatively simple, but robust, sensors. Very good isolation from vibration from engine, transmission and rotorsystem increases the quality of sensordata and the lifetime of the sensors and electronics.
FCS 202 consists of a computer, a number of sensor and a power supply unit. The mainpart of the FCS 202 is packaged in a central unit which is to be placed vibration isolated in the inertial center of the carrier. The central unit is complemented by a number of decentralized sensors mainly located to the tailbar.
The software of the FCS 202 is developed for fully autonomus flight control with indata from optional sensors. The extremely open arcitecture make the system very open to adding functionalities, for example active vision and higher levels of intelligence.
By qualified filtering and well balanced regulators the FCS is able to control the carrier with extremely high precision also by using relatively simple, but robust, sensors. Very good isolation from vibration from engine, transmission and rotorsystem increases the quality of sensordata and the lifetime of the sensors and electronics.
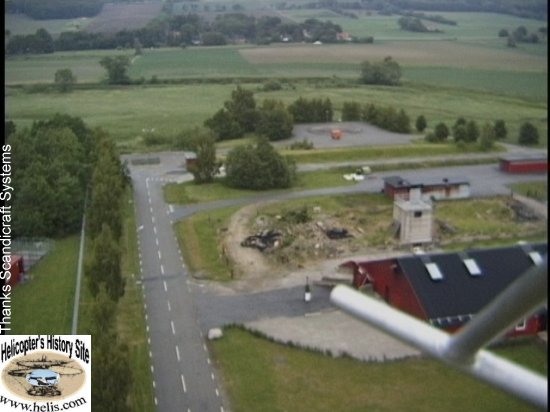
Data och performance:
Computer: PC-104 based Ampro-586
Max IO-kanaler: 32 analog, 32 digital, 6 serial and 10 timers
Realtimesystem: RTKernel 4.5
Softwaretool: Systembuild
Codegenerator: AutoCode/C
Sensors: 1 inertial navigation package (3 gyros, 3 accelerometers) , 1 2-axis inklinometer, 1 Compass, 1 GPS-reciever, 1 Microwavealtituderadar, 1 Infraredaltitudemeter, 1 Barometer, 2 Revolution counters, 1 Fuelmeter
Ground Control System GCS 202
The GCS 202 consists in the standardversion of a computer and a communicationlink between the carrier and the ground station. The computer works as a communication central for supervision of and communication with the carrier and its payloads. A tailormade communication protocol creates an efficient interface easy to use.
The GCS 202 is intended to be housed in a covered trailer for a private car (not included in the offer).
The GCS 202 consists in the standardversion of a computer and a communicationlink between the carrier and the ground station. The computer works as a communication central for supervision of and communication with the carrier and its payloads. A tailormade communication protocol creates an efficient interface easy to use.
The GCS 202 is intended to be housed in a covered trailer for a private car (not included in the offer).
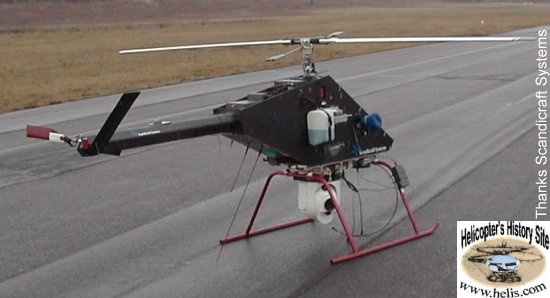
Extra options for GCS 202 are for example:




Data and performance: Computer: Intel-486 industry computer
Datalink: 9600 baud radiomodem (439MHz)